Turning processing is a form of machining, a material removal process, which is used to create rotational parts by cutting away unwanted material.
The turning process requires a turning lathe or machine, workpiece, fixture, and cutting tool. The workpiece is a piece of pre-shaped material that is secured to the fixture, which itself is attached to the turning machine, and allowed to rotate at high speeds.
The cutter is typically a single-point cutting tool that is also secured in the machine, although some operations make use of multi-point tools. The cutting tool feeds into the rotating workpiece and cuts away material in the form of small chips to create the desired shape.

The turning process is often used to process bar or rod-shaped materials. Finished parts are usually called precision turned parts, suitable for Simple turned parts processing, shaft turned parts machining, sleeve turned parts processing, disc turning parts processing, complex turned parts processing, CNC turning parts processing.
Turning is another of the basic machining processes. Turning produces solids of revolution which can be tightly toleranced because of the specialized nature of the operation. Turning is performed on a machine called a lathe in which the tool is stationary and the part is rotated. The figure below illustrates an engine lathe. Lathes are designed solely for turning operations, so that precise control of the cutting results in tight tolerances. The work piece is mounted on the chuck, which rotates relative to the stationary tool.
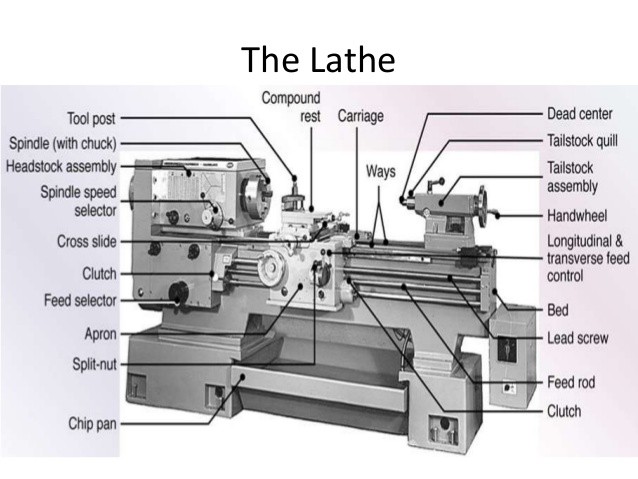